The butt welding machine is a dedicated welding equipment that applies hot melt butt welding technology to weld thermoplastic pipes and fittings. The welding frame and operating system of the hot melt welding machine are separate. Depending on the method of use, it can be divided into five major types: manual, hand-operated, hand-push, hydraulic semi-automatic, and CNC automatic. Each type is selected based on different welding environments and operational conveniences.Next, let’s introduce how to actually use a butt welding machine
Step 1: Preparation
- 1 Confirm the pipe size and wall thickness, and select the appropriate specification of the butt fusion welding machine.
- Place the butt fusion welding machine on a flat and stable surface, connect the power supply, and preheat the welding joint and pipes.
- Prepare the hot melt fusion joint, cleaning cloth, wrench, and other tools.
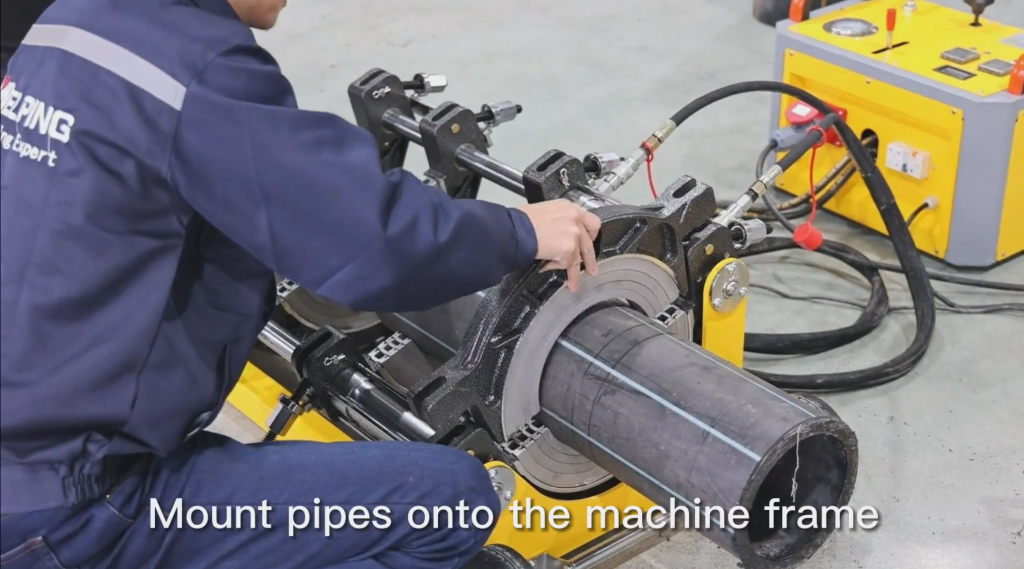
Step 2: Pipeline Preparation
2.1 Assemble the hot melt fitting onto the pipe port, making sure it is aligned with the outer contour of the pipe.
2.2 Close the upper and lower brackets of the docking frame and fix the PE pipe with bolts.
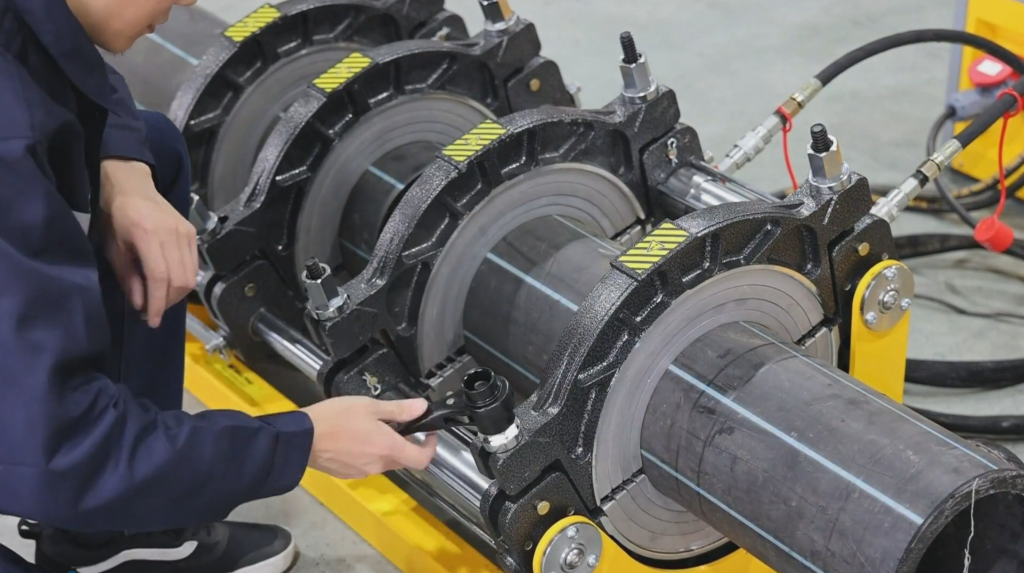
Step 3: Welding operation
For milling, take the milling cutter out of the basket and place it between the two PE pipes. Push the joystick of the hydraulic station to contact the two PE pipes with the milling cutter until the two connecting planes are milled and a continuous long strip is milled out. crumbs.
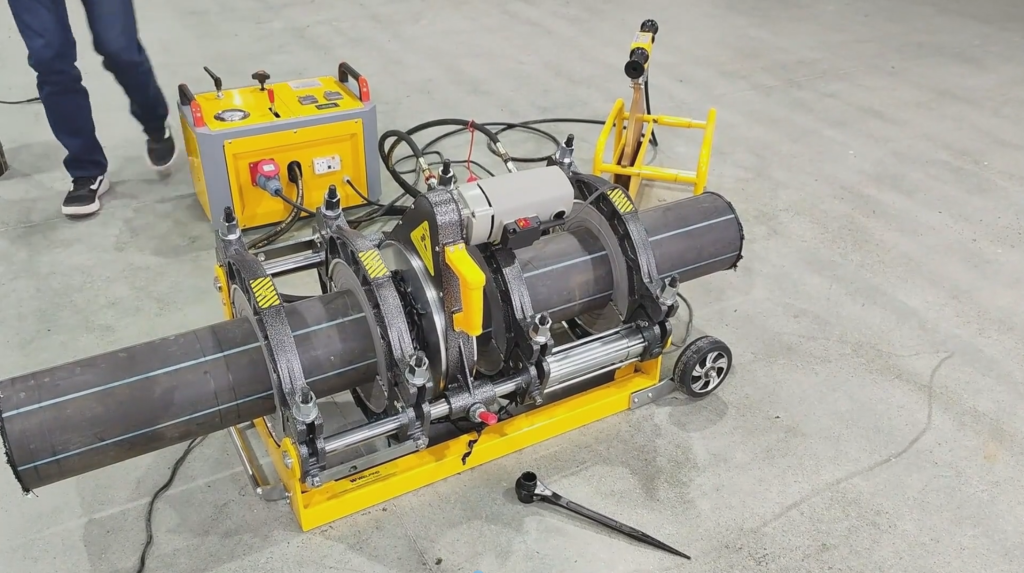
Heating, put the milling cutter back into the basket, take the heating plate out of the basket and put it between the two PE pipes for heating. After the two pipes start to flange and meet the requirements, put the heating plate back.
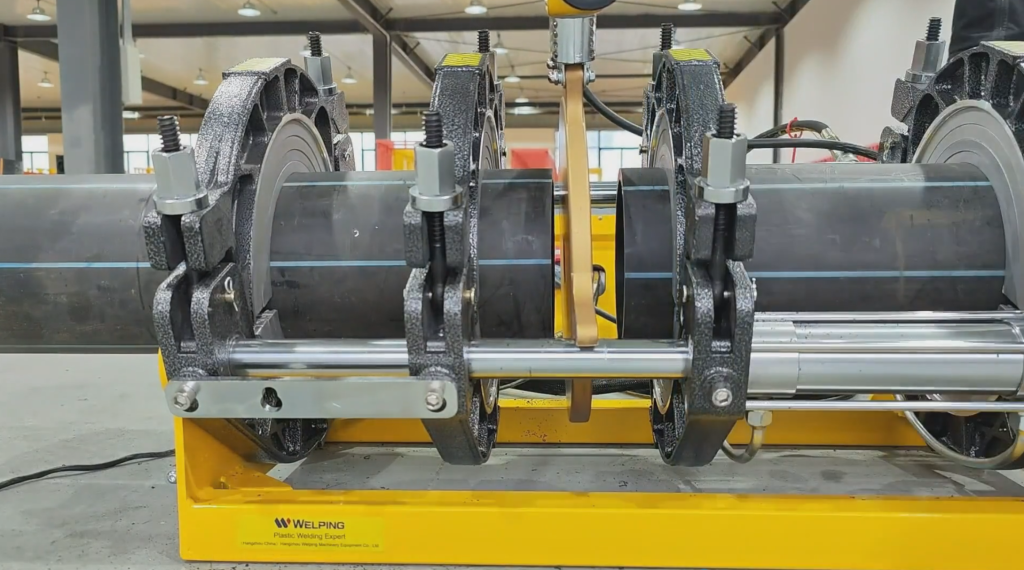
For welding, after taking out the hot plate, immediately press the required pressure to quickly close the PE port to be welded.
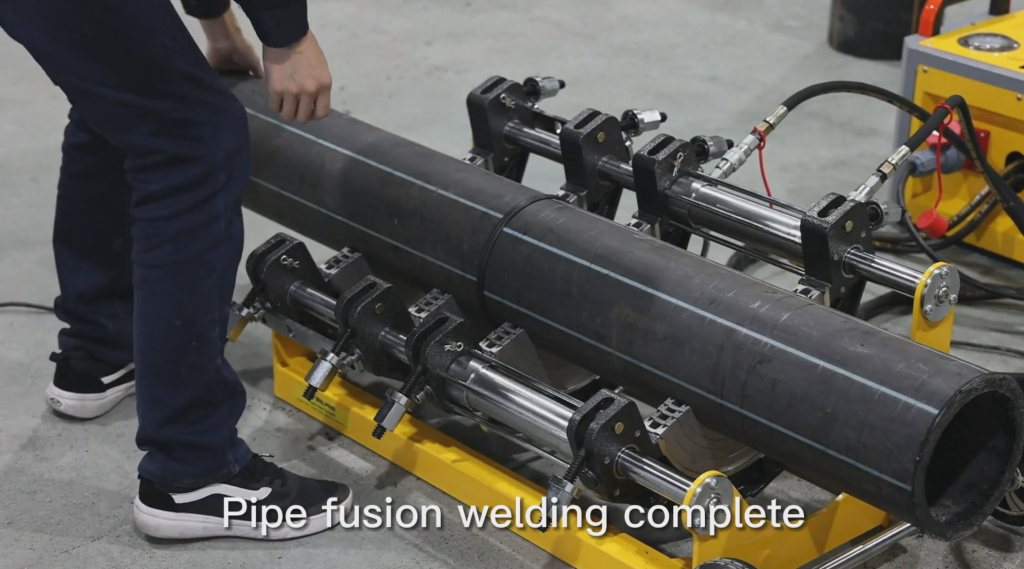
Step 4: Acceptance Inspection
- Check whether there are cracks, bubbles and other defects in the hot-melt welding joint.
- Use a pressure tester to perform a pressure test to ensure that the connection is tight and there is no leakage.
- If problems are found, repair them in time and conduct acceptance inspection again.